Many logistics employees are familiar with the situation: The working day flies by in the face of multiple tasks. You’ve barely started in the morning when the clock shows it’s almost noon. And when the workload doesn’t diminish in the late afternoon hours despite all the effort, some people wish the day had more hours.
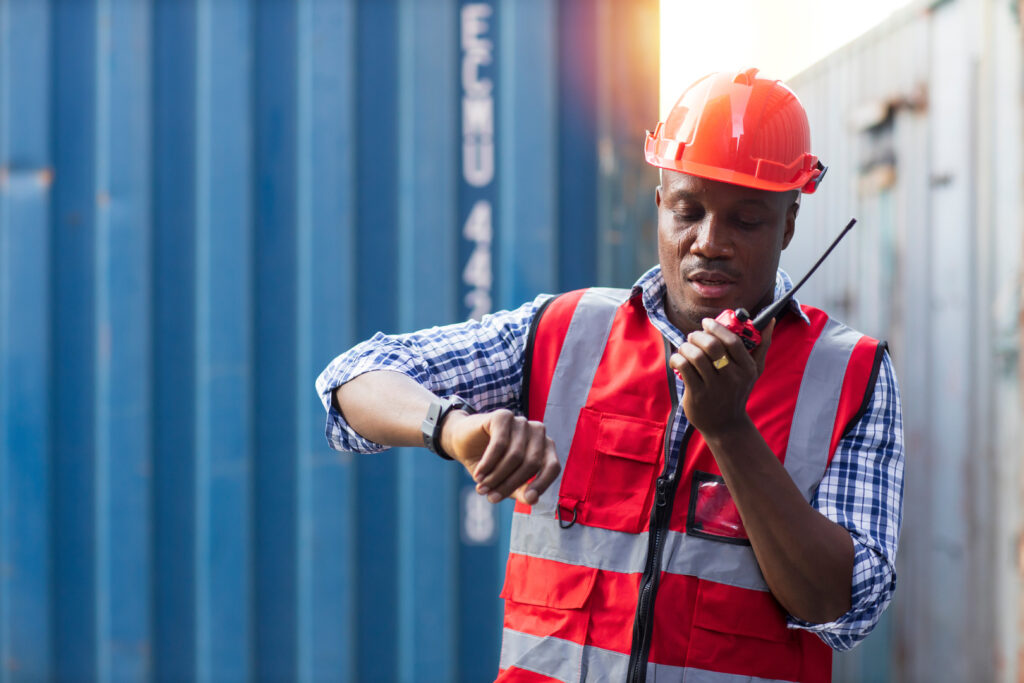
Even in normal times, logistics often represented and still represents the “stress peak” of most possible industries. During the pandemic, however, when the workload increased by several degrees, especially for logisticians involved in mail order, stress levels also reached previously unthinkable new heights.
The problem with this is that stress as “tension of the body” can be increased at will. However, the human ability to endure and cope with it is limited. The faster our “accumulators” are drained and the fewer opportunities there are to replenish them, the greater the loss of performance. This in turn results in even more stress to fill the gaps – a downward spiral that ultimately ends in the dreaded burnout.
An illness that is still often misunderstood in its massive effects and therefore frequently underestimated. Anyone who has experienced real burnout will not only need long months of therapy, but will never again be able to call up such performance. A person literally “burned out” – lost forever to the entire logistics industry as a valuable workforce.
Combating stress is the key to countering this. And it is clearly more than “just” maintaining inner balance. It is a direct investment in a constantly high performance of valuable employees. Because those who do not experience stress in excess over the long term are demonstrably more satisfied, more efficient, more productive and less prone to error – and ultimately this should be the fundamental concern of every manager.
Stress prevention versus stress management: Terminology
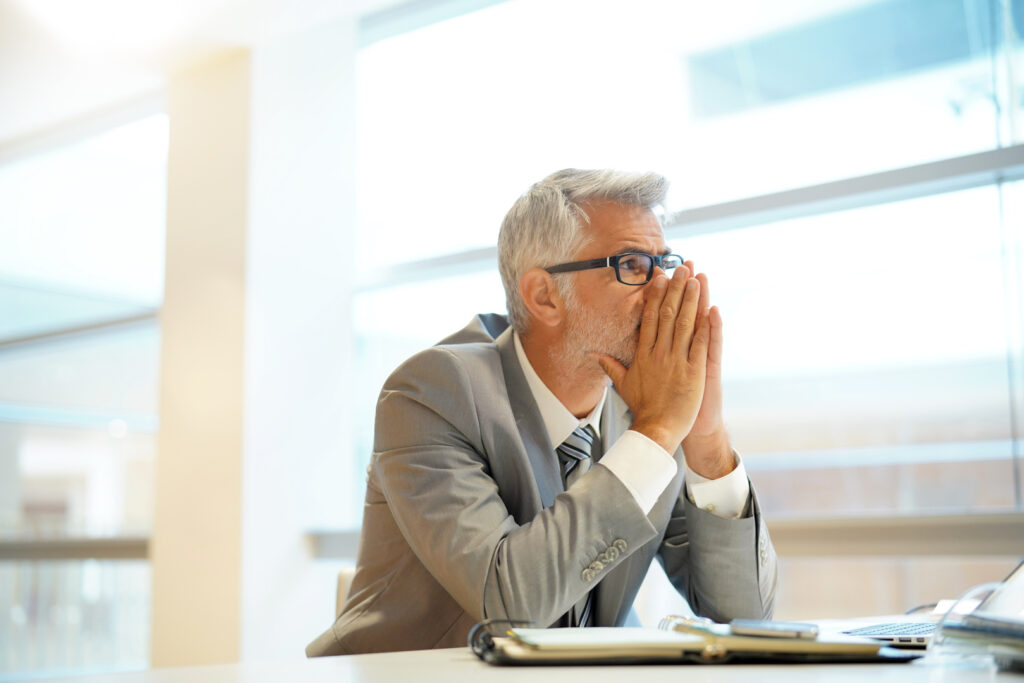
Under the umbrella term stress management, there are several terms that are often used incorrectly-synonymously or completely out of context. The four most important terms that everyone should know are:
- eustress: a “positive” stressor that can considerably increase performance over short periods. This stress can be easily balanced without special measures.
- disstress: a “negative”, i.e. permanently overdrawing the conventional performance and regeneration capacity, (eu-)stress. It requires consistent compensatory measures. This is the dangerous stress from which many logisticians suffer.
- stress avoidance: The fundamental attempt to consistently prevent any form of (dis)stress at the onset.
- stress management: The opposing attempt to cushion the effects of negative stress after the fact – to recharge the “batteries.”
In other words, eustress is not a problem in logistics work, but the opposite. Similar to an escape situation, people can perform better over certain periods of time and are more alert and productive.
All measures should therefore be aimed at maintaining performance capability for normal (stressful) day-to-day business and, at the same time, ensuring sufficient performance capability to maintain a “booster” function during times of special peak demands.
Stress prevention: Key methods
From a psychological point of view, the best approach to combating stress is to allow as few stressors as possible to arise in the first place. This even applies to eustress. Even this positive stress should only be built up if really necessary, as it can quickly turn into disstress. Stress avoidance aims at this. However, the term by no means only refers to a reduction of stress.
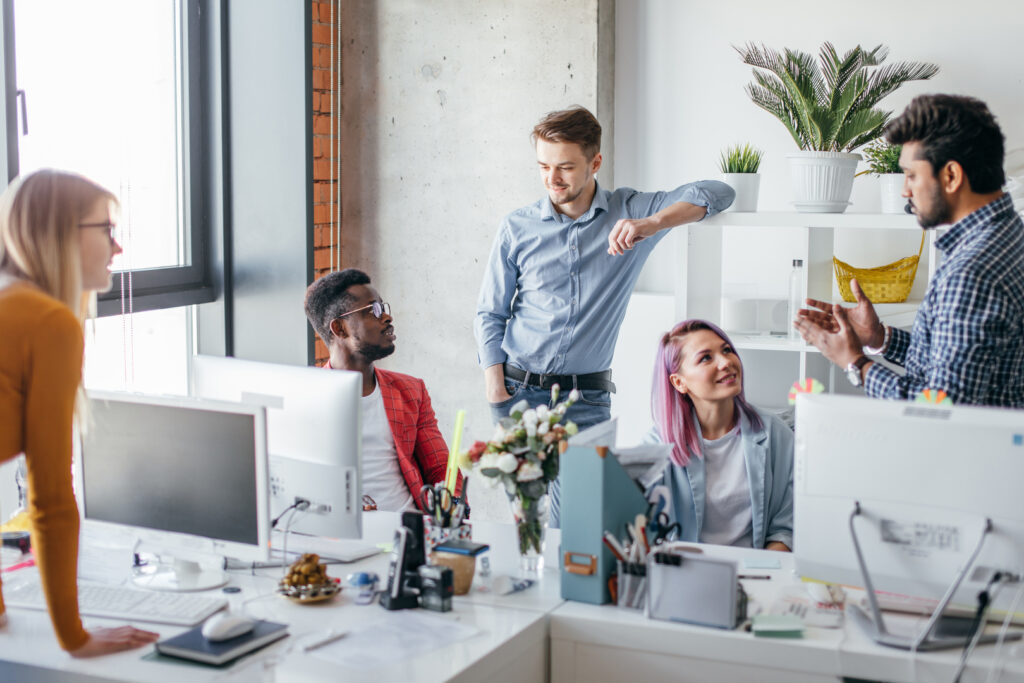
Resilience: How susceptible a person is to stressors depends to a maximum extent on his or her thinking and attitude. For this reason, an experienced dispatcher, for example, can withstand significantly more “pressure” than a novice.
However, resilience is only partially related to habituation. Rather, there are seven scientifically recognized pillars behind it. They can be trained with targeted exercises – for this purpose, further training measures for the team are definitely offered in the operational environment. Stress can also be avoided by changing the language used: “Could you please…” instead of “You must immediately…” is a well-known example of this.
Time management: Every day has only 24 hours. Only a fraction of it may be legally used for work. In this respect, it would be wrong to fill those eight hours with as much work as possible – in fact, this is one of the most important triggers of disstress. The right thing to do, however, is to strive for smart time management.
The absence of time pressure is important for this. Every employee should be allocated the appropriate amount of time for a task – as difficult as this can be in our industry. Moreover, it is important to always plan with sufficient time reserves. No less important is the division of tasks into blocks of time. The more the brain has the opportunity to focus on a task (instead of being constantly distracted), the lower the stress level. Accordingly, a policy of fixed responsibilities and task assignments should exist in logistics operations.
Personnel policy: each person can only perform at a certain level on a sustained basis before stress becomes detrimental. An important key to this is the staffing level available at his or her workplace. This is because too much work is often distributed among too few personnel for reasons of economy. As a result, the entire team is permanently overloaded, an entire department or even the company suffers. A far-sighted personnel policy therefore not only looks at the costs caused by each individual employee. Above all, it looks at the long-term revenues that each employee brings in. Accordingly, there should be a “healthy” staffing level. However, it should be emphasized that more staff should not be an invitation to increase the volume of orders. Because then the problem starts all over again.
Overtime policy: The legal framework for overtime is extremely clearly regulated and intentionally leaves certain(!) leeway. Often, however, it is not the supervisors who are the problem here, but employees themselves.
- Poor time and task management,
- Competitive situations between employees,
- recognition and promotion desires
in combination with wrong-thinking superiors often lead to completely avoidable stress. This is definitely a matter for management. It must pursue an extremely consistent policy. One whereby “voluntary overtime” is not viewed positively, but the opposite. Once again, many decision-makers have a hard time with this; in many companies, such behavior is still viewed extremely positively as a special effort.
Stress management: Important methods
It is often very difficult, especially in our industry, to consistently implement the aforementioned avoidance strategies – behind them are too often intertwined realities of logistics in and of themselves.
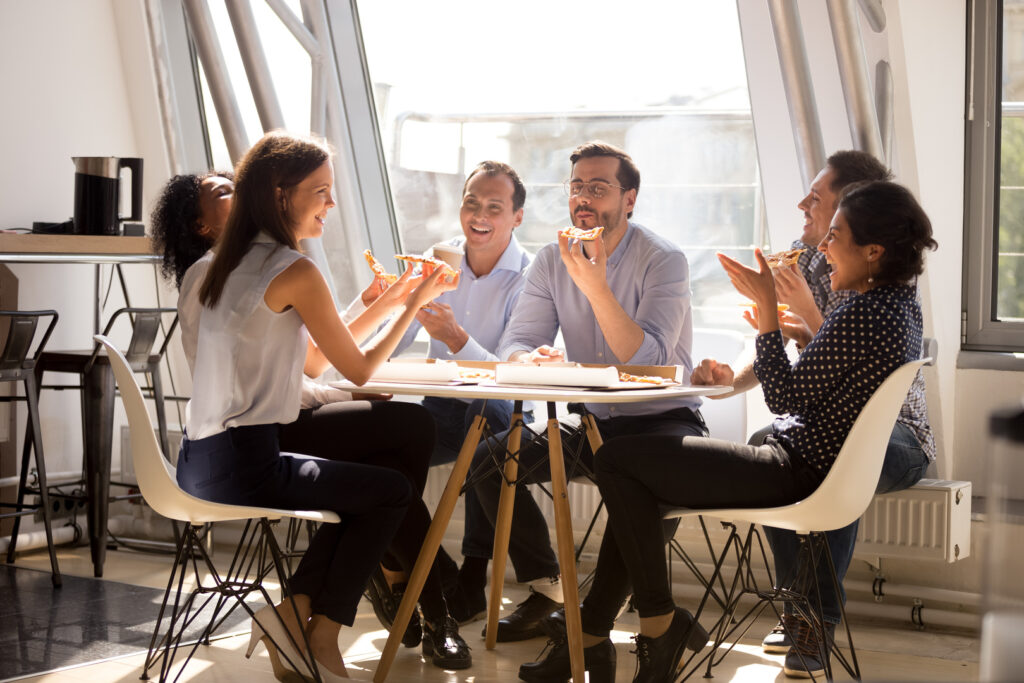
If, however, it is not possible to prevent negative stress before it arises, then it is really necessary, with a view to the person and the competitiveness of the company, to try to reduce any stress that has arisen in a timely manner. The problem with this is that some of it falls into the area of leisure time and is therefore beyond the employer’s control.
Clear break regulations: There is a reason why breaks are explicitly mentioned in working hours. However, especially in offices, many employees have become accustomed to spending them at the workplace. While this is a break according to the legal definition, it is not from the more important psychological point of view.
The brain must be given time to forget about work. Therefore, a) there should definitely be a break room, b) breaks (in a shift) should be taken by everyone together if possible, and c) managers should definitely make sure that these breaks are taken in a meaningful way. As with overtime, there should be neither tolerance nor positive reinforcement of negative behavior.
Sufficient sleep: Sleep is by far the most important weapon against the accumulation of harmful stressors. This is because numerous cleansing processes take place in the brain at night, and important information is also transferred to long-term memory. Of course, there’s little employers can do about this except to ask their employees. But they should do so emphatically.
After all, employees who get the amount of quality and quantity of sleep they personally need each night automatically reduce stress that would build up even if they took other measures.
A “duty is duty” policy: Logistics is an industry in which work is mostly done around the clock. However, managers should always keep in mind the effect on the psyche of not being able to get work out of one’s head, even after hours.
In view of this, companies should consistently try to allow employees of all ranks to rest in the evening. This is especially true when it comes to the issue of accessibility. Put simply: Those who are off duty should not be bothered, except in genuine emergencies.
Ultimately, there are numerous other measures to be mentioned here between sports, meditation as well as the avoidance of additional leisure time stress. However, these are things that employers have no control over. However, there should at least always be an attempt to make the team aware of the possibilities and consequences after hours. When this is met with a stress-avoiding and otherwise stress-reducing work environment, the needs are usually met, even in an industry as hectic as logistics.