Imagine you wanted to move your TV at home. However, there are no sockets in the new location and you don’t want to work with extension cables. Would you then courageously grab a hammer and chisel, chisel cable slots into the wall and install new sockets in the desired location? After all, you may already have experience with connecting ceiling lamps, and the technical and mental leap doesn’t seem that far.
If you answer in the negative, you have most likely already grasped an important core: Just because you have mastered a task does not automatically mean that you can also manage similar but much more complex tasks on your own. This is also true in your logistics business. Even if you are an experienced business owner and lead a team of really capable people, there are still tasks for which you are better off hiring external professionals – simply because they are more experienced, more focused, more professional in these segments. In fact, this is also a form of thriftiness: you have to pay these external people more, of course, but in return you get higher quality work, sometimes much faster.
- maintenance and conversion of your vehicles
If your company owns lorries, it is possible that, due to their size and complexity, little work is done on them in your company; just fitting the required winter tyres on lorries is a feat of strength that can hardly be compared with the procedure for smaller vehicles. However, if you (also) have vans, regular cars and other (smaller) vehicles, you may well want to do work on them in-house.
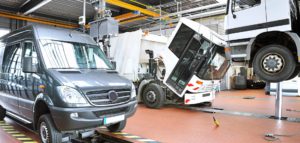
Maybe a brand new Sprinter needs an interior fitting with shelves for parcels; an older van needs to be inspected; a forklift needs its brake pads replaced. Depending on the equipment and background of your team, it may seem appropriate to do it yourself.
But that is exactly what you should not do. The risks are great:
- when removing and installing parts, it can quickly happen that the threshold for work requiring approval is exceeded. The vehicle then loses its permission to participate in road traffic.
- even simple vehicles are highly complex today. It is easy to overlook things due to ignorance, to damage something or to omit work – for the latter, think of the multiple working positions of a superficially simple inspection.
- many jobs are safety related. If they are not carried out with the highest level of (model-specific) expertise, major hazards can result.
Finally, you should also bear in mind that you have a warranty claim if the work is carried out externally. The liability for defects is transferred to the company carrying out the work, you yourself can insist on this in case of doubt, where your company cannot hold anyone accountable for its own mistakes.
- testing and integrating new digital techniques.
A good logistics company has at least one employee who (also) knows about IT. He knows what computing power your company really needs, can set up and operate servers and the company network, create the company websites, or at least maintain them. Perhaps there is even a regular IT department dedicated to these tasks.
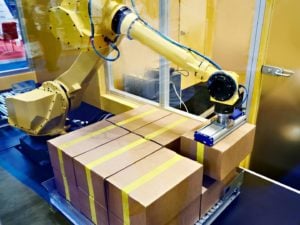
Their work, however, should end where it concerns digital technologies with which your company has had no contact so far. Perhaps you want to integrate forecast-based supply chain management or related applications of Logistics 4.0; perhaps your company should also benefit from the multiple advantages of the new technology, which is summarised under the term Edge Computing and which is currently establishing itself in logistics and industry as an important approach to optimisation, flexibilisation and increased reliability.
Such tasks are “also IT”, but they differ from normal office and logistics IT about as much as the engine of a lawn mower differs from the engine of a tractor unit. Here you should delegate the following to outsiders:
– Examine the general needs in your company.
– Specification of the scope required here.
– Selection of the relevant components.
– Installation of the entire system.
Of course, you should also use these professionals to have your own IT people trained at least for operation and rudimentary troubleshooting. Training is also the key word here, which leads us on:
- train and upskill your staff.
Your company probably also uses a version of Microsoft Office for everyday office tasks. But hand on heart: does everyone in your team really know all the details of Word, Excel and Co. so intimately that they have a complete command of the programmes?
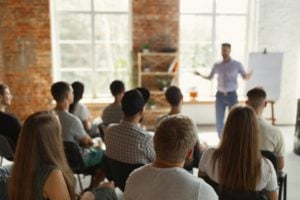
Or what about when you purchase a completely new model of forklift truck: Does the procurer simply pass on the manufacturer’s key data to the operators, but otherwise trusts them to find their own way around, or do your people receive training from the manufacturer?
There are countless such examples. They range from training new drivers who have never worked in logistics before, to new laws affecting your accounting staff, to low-level and high-level IT.
Admittedly, there are training topics that an experienced company full of capable employees can absolutely handle on its own. But there are also figures like this: 95 per cent of all logistics professionals believe that their company has some catching up to do when it comes to the digital skills of their employees. Countless other statistics prove that employees very often feel left alone when it comes to introducing new techniques or expanding existing things.
For you, this should be food for thought: Not only, but especially in IT today, there are hardly any simple, self-explanatory innovations. Today’s development processes are extremely fast and usually very profound.
– General range of functions of the applications you use;
– New functions with updates;
– Newly implemented programmes and other IT products;
– Cybercrime and IT security;
– Changes in legislation;
These topics should be reason enough to have at least one employee who is affected trained externally, but fully on the topic. However, you should choose this employee very carefully – he or she must also have the ability to pass on what he or she has learned to all other team members. Only such external training guarantees that everything is really explained by professionals and that no mistakes slip through.
And when it comes to topics that affect a large part of your staff, let’s take a brand new operating system as an example, or even a brand new office software that is used by most, then you should not hesitate and prescribe an “education day” for your entire team. On this day, an in-house training session will be conducted by an external specialist – of course, you as the managing director should not take time off from this appointment either.
- energy saving and regenerative energy production
Electricity and heating energy make up a considerable part of the operating costs in every company, of course also in logistics. The desire to make as many adjustments as possible is therefore understandable.
Perhaps you have also noticed how many guides there are on this topic on the web. They advise, for example, replacing light switches with motion sensors, connecting IT to master-slave sockets or even covering the company’s halls with an armada of photovoltaic panels.
Admittedly, in principle there is nothing wrong with all this advice. However, they usually lack one important point at the core: they are necessarily formulated too universally. Companies, however, differ from each other in countless details.
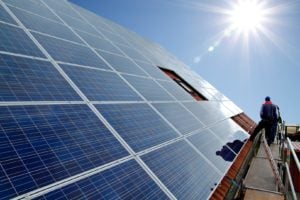
Take light sensors as an example. Of course, you could (have) them installed in washrooms and other areas that are not permanently used. This would eliminate any danger of an employee leaving the light on unnecessarily. But what if your work in such rooms is often of a non-moving nature? Then literally “the lights would go out” above your people. Work processes would be disrupted, perhaps safety would be compromised.
And as far as photovoltaics are concerned, there are no universal solutions between the load-bearing capacity of roofs and the general orientation depending on the cardinal directions.
This means that you should hire energy experts for such measures. Only they have the necessary expertise to:
– recognise what is technically feasible in your company;
– find out what actually makes sense in your company;
– communicate in which way what should be applied.
Only in this way can you achieve energy efficiency that actually benefits your company and does not disrupt processes – because here, too, there are big differences between maximum efficiency and sensible efficiency.