The 2030 scenario of the German Federal Ministry of Transport and Digital Infrastructure sees a rapidly increasing interlinking of transport modes, improved transport flows and significantly increased transparency of supply chains. The increasingly digitalised transport management is supported by artificial intelligence, so that vehicles and infrastructure can largely manage the transport routes themselves.
For the logistics and transport industry, this future is a huge challenge. It has to move, because the advancing digitalisation of the entire economy means nothing less than that forwarders and transport companies – keyword Logistics 4.0 – can only count on orders in the future if they offer a digital structure for communication that can be integrated into the client’s IT system via appropriate interfaces. Without this possibility, even medium-sized transport companies and freight forwarders will not be able to keep up with the competition.
Creating the prerequisites
So it is becoming clear that forwarding companies will have to cope with an ever-increasing number of logistics services. At the same time, they must always be one step ahead of the competition. However, the prerequisites for this still have to be created in many places, because communication between shippers and transporters or forwarding companies is still organised in analogue form in many cases – for example at the loading ramp. Delivery notes and pallets of goods change hands, signatures are made and filed in multiple copies. In these work processes, digitalisation of the supply chain is often nowhere in sight.
Why is this the case at the ramp? The fact is that the real transition from incoming or outgoing goods to the transport vehicle with all the necessary information, agreements and detailed regulations is relatively complex. All this is the subject of communication between the warehouse employee and the driver of the executing forwarding company or a subcontracted transport company. Much, if not most, is recorded manually. Of course, there is also a digital solution for this, for example by transferring the data from a warehouse management system (WMS) to a transport management system (TMS). But even if the prerequisites for this are available on both sides, there is often a lack of appropriate interfaces. This means that the systems cannot communicate with each other. Then only forms and hand-made lists can help. But it is also clear that time will pass.
Interfaces for the supply chain
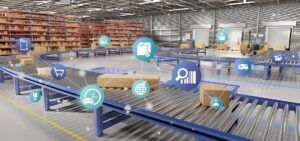
The interfaces are becoming increasingly important. They are of central importance for the entire process of digitalisation. This is by no means just about such relatively small problems as communication and data flow at the loading bay. The goal is more complex. It is about the end-to-end digitalisation of the entire supply chain, starting with the procurement of materials and warehousing by the goods manufacturer, through the entire process of production to the storage of the goods and finally their dispatch via likewise digitally integrated forwarding agents or a transport company and delivery to the customer. At the end of the development is a digitally managed and controlled, completely paperless supply chain – fast, effective, transparent. Logistics must link up with these largely automated processes. Because the information chain in general, and especially between the office and the driver, must not break where efficiency and speed are important.
The driver as a weak point in the supply chain
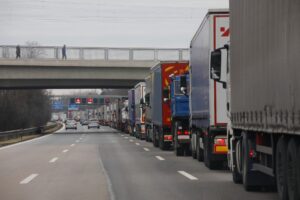
This is precisely where the logistics industry encounters a problem that it itself freely admits: the driver is a weak point in the supply chain, for various reasons. Drivers hired from other countries replace a lack of German specialists, which leads to communication problems. Low pay in many haulage and transport companies makes for disproportionately frequent staff turnover. Instructions that are not understood due to language barriers make consistent communication and the associated exchange of data difficult. In addition, there are often overcrowded traffic routes and traffic jams that literally stand in the way of the goods arriving on time. Here the chain breaks again.
Mobile tools
Today, many freight forwarders and transport companies already use mobile aids: on-board computers, for example, help to provide information, simplify the exchange of documents by using printers in the driver’s cab and make transport planning more flexible overall. Special apps are also used for communication and can be supplemented by video telephony – for example, if damage has occurred to the truck and this needs to be documented visually during a telephone call with a foreign workshop. Image translators via app can also make it easier for truck drivers of different nationalities to communicate with each other when the spoken word cannot help. Here, catchy symbols are displayed on the smartphone with which a driver can express his concern. Via messenger services such as WhatsApp, the drivers keep in touch in chat groups not only with the dispatcher, but also with each other.
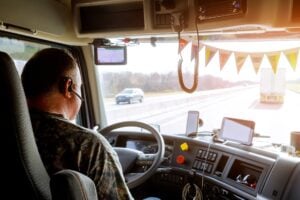
The new “digital driver’s office” is another approach by logistics companies to close gaps in communication and the flow of information between all those involved in the process. This can relate, for example, to accidents or unpredictable absences due to illness. The Digital Driver’s Office takes the driver by the hand electronically, so to speak, with the help of an app and guides him step by step through the necessary documentation, which is transmitted to the head office in real time and can thus be made available to all those involved in the process. It is a kind of “interface light” that cannot replace a missing interface, but can bridge the gap more effectively than with the old methods. Such and other digital processes make the work of truck drivers easier. And they are also more and more attributes for an attractive job for the new generation of truck drivers. As they have to deal with ever-increasing demands during their daily work – such as traffic jams, time pressure, communication difficulties – mobile aids can also be a real relief in these respects.
Mobile workflow management also simplifies status communication between drivers and dispatchers when apps calculate the driver’s estimated time of arrival. Such apps can also automatically translate the necessary work instructions into the required foreign language, which additionally facilitates communication with foreign colleagues, because the functionality of the apps allows the dispatchers and drivers involved to communicate in their native language. And: With the use of this IT technology, sources of error and misunderstandings can also be reduced when truck drivers are digitally guided through their daily work routine.
Direct communication increases efficiency
These and other mobile solutions enable employees to communicate in real time and connect everyone, regardless of whether they are processing, managing and documenting orders in the office, working as commercial employees in the fleet or on the road as drivers. For the drivers, mobile apps bring an invaluable advantage: communication between them and dispatching is largely eliminated. Enquiries about the exact position of the delivery vehicle and the presumably remaining driving time, the expected arrival at the customer’s premises are handled electronically with the help of a live map and the arrival monitor.
Direct communication between dispatchers and drivers based on such electronic tools serves to increase efficiency in the entire order processing – for example, by exchanging data to check the progress of the order. There is a whole range of such corresponding communication systems and they are constantly being further developed. These dock onto existing computer structures of forwarding companies. Because of the different work processes and structures in forwarding companies, appropriate software should ensure that the communication system can be easily adapted to company-specific work processes.