The best, most flexible and cheapest warehouse is undoubtedly one that is not needed at all. This is the main reason why just-in-time manufacturing has taken hold in manufacturing companies in particular and has global significance today. However, the principle is simply not optimal for every industry – or even feasible at all.
In such cases, warehousing is an indispensable part of the entire entrepreneurial activity or even its core. However, this does not at all mean that there is no room for optimization in terms of increased flexibility. The following tips prove this in detail.
Why the modern warehouse must be flexible to the maximum extent possible
Today’s world has become extremely fast-paced and thus less precisely predictable. This is especially true in the corporate world. This makes unforeseen events at least more likely – with the pandemic and the upheavals caused by the Ukraine war as probably the most prominent examples of the recent past.
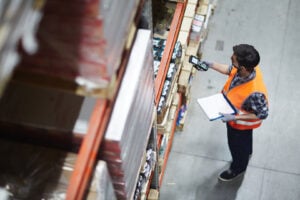
In principle, there are several points at which disruptions can occur, from the manufacture of the individual parts of a product to its delivery to the end customer. Globalization plays a major role in this – even if it can offer many advantages elsewhere.
In addition to such potential (and multiple) supply chain disruptions, there are other positions today, such as:
– faster-moving and more volatile customer interests or loyalties,
– lower profit margins and thus less financial leeway in the form of reserves,
– greater seasonality of goods or interest in them, and
– Shortage of skilled labor and resulting changes in employee behavior.
All this and more can not only push an inflexible warehouse to its limits, but also turn it into a downright damaging factor in a company. For example, when an enormous amount of “dead capital” in the form of goods is tied up due to insufficient flexibility. Or when the entire warehouse organization makes it difficult or impossible to react quickly to rapidly increasing demand.
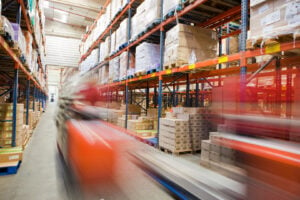
stock.adobe.com © Chlorophylle
A modern warehouse must therefore be able to provide as much flexibility as possible. Only then can it adapt to different events – without losing the ability to react to other events. In concrete terms, greater flexibility results in three strong advantages that can provide answers to all of today’s challenges:
- transparency: real-time information is constantly available. This means that every item can be fully tracked and traced. There is never a threat of confusion and further difficulties triggered by it.
- adaptability: a flexible warehouse can adapt to changing market conditions on both sides of the supply chain – at short notice and at the lowest possible cost.
- increased efficiency: the entire planning and process chain is simplified and accelerated, as the flexibly positioned warehouse allows different throughput speeds.
It should be emphasized that these are only “upper groups” of advantages, so to speak. Each of them has several other associated benefits – such as lower costs, more revenue and less dependence on staff. But what can entrepreneurs practically do in this regard?
Constantly check the bearing layout
Whether it’s the spare parts warehouse of a craftsman’s business or the huge shipping warehouse of an online retailer: every warehouse has only a limited total area. It consists of
– The actual storage space, e.g. for shelving,
– the absolutely necessary circulation areas in between,
– the area for picking and packing or other preparation for shipping, and a loading and unloading area.
– a loading and unloading area.
This means that only part of the total space is reserved for storage. The rest, on the other hand, is needed for the other processes that are absolutely necessary for storage.
This space is fixed. An extension is possible, but – for example, in the case of an annex or a hall extension – it is at least associated with very high costs. If the company does not own the necessary expansion space, it must be purchased additionally. This is always expensive and may even be completely impossible for various reasons.
However, spatial expansion should always be considered only as a last option. Because in terms of layout, much can be done even on the same space to make processes more flexible and/or speed them up.
Tips and best practices
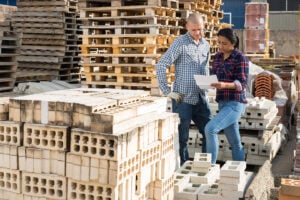
stock.adobe.com © JackF
At the core of an optimized warehouse layout are two things:
- Shorter distances and overall increased work speed – especially for goods with a higher throughput rate.
- Maximum utilization of the existing storage areas.
For this purpose, it is highly recommended to always consult the warehouse management software used or to purchase software that contains an integrated supply chain analytics tool.
With such a tool, the large data sets can be used to find out very quickly whether the warehouse as a whole is adaptable – and where things sometimes get stuck. Based on this, the layout can be improved, primarily through the following measures:
– Changing the workflow: depending on the architecture, V-, I-, L- and U-shaped approaches are suitable here, with the ends of the “letters” representing the unloading and loading areas respectively. Depending on the type of goods and again building architecture, a redesign can bring a significant improvement.
– Changing the type of storage: A rough distinction is made between static and dynamic storage. While in the former, each item always has a fixed storage location, in the latter, sorting takes place depending on how and where there is space at any given time – which is why dynamic storage is also referred to as “chaotic storage”. It can hardly be implemented without a powerful warehouse management system, but it has been proven to offer significantly increased flexibility and full utilization of space at all times.
Last but not least, it is important to simulate different approaches concretely for quite unrealistically high utilization times. This is the case when not only a large number of pickers are on the move, but also when enormous quantities of goods are constantly being stored and delivered.
Make working hours more flexible to the extent legally possible
Warehouse personnel, or rather the legal working time and break regulations that apply to them, are often an obstacle on the path to greater flexibility. Because:
- within a six-month period, the average daily working time must not exceed 8 hours.
- there must be an uninterrupted rest period of at least 11 hours between two work units.
- there are very high hurdles for employment on Sundays and public holidays. In addition, courts have ruled several times that not every high volume of work justifies exceptions – including against Amazon.
This and a few other points can make it very difficult to have enough staff in the warehouse for peak times. However, there are certainly ways to stay within the bounds of legality and still be able to absorb both phases of very high utilization and those of the total opposite.
Tips and best practices
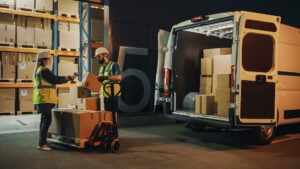
stock.adobe.com © Gorodenkoff
The following approaches are primarily suitable for this purpose:
– Ordering overtime with appropriate compensation – this is interesting in that the compensation can be legally secure financially or in terms of time. For example, it is possible to let employees accumulate overtime during peak periods and then reduce it by order. Here, reference should be made to the regulation: The daily 8 hours only have to be worked on average over half a year or 24 weeks.
– Firm cooperation with temporary employment agencies – especially those that are geared to placing experienced warehouse personnel.
– Building up a permanent pool of flexibly deployable “seasonal workers”. Many people exist here who only need such work on a temporary basis and actually appreciate the flexibility it offers.
– Ordering shift work is possible in principle with legal certainty under certain conditions. Likewise, it is quite possible to do this shift work only for short periods of time and then return to a conventional model.
Ultimately, many things are feasible even within the framework of the legal requirements if the works council and employees play along. Experience shows that the chances of this happening increase if employers are fair in this respect. That means paying employees for extra work and actually sending them home when there is little to do – instead of frantically trying to find alternative work.
Use more easily deployable and replaceable storage aids
The term storage or loading aids covers everything that helps to move goods more easily, to store them or to combine them into units that are easier to handle.
The challenge from the point of view of an overall more flexible storage area consists of a discrepancy:
– On the one hand, storage aids must always be available in sufficient quantities – and as spontaneous as possible, so that it is possible to react quickly to increasing changes in demand.
– On the other hand, the same storage aids should take up as little space as possible when not in use, so that no valuable space is lost for actual goods.
In many companies, therefore, there is no way around setting up a regular “warehouse for storage aids”. This may be necessary, but in practice it complicates many things. This is because, by its very nature, such a “warehouse within a warehouse” must be integrated just as correctly into the overall processes.
Tips and best practices
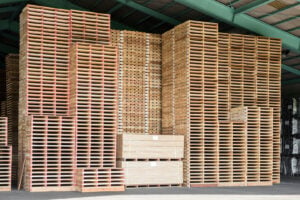
stock.adobe.com © lastpresent
Compared to other options in making the storage area more flexible, there is only one really viable solution here: to rely as extensively as possible on storage aids that take up as little space as possible when unused, yet have comparable load-bearing capacity and handling to more conventional aids.
Particularly in covered warehouses, corrugated storage bins offer several interesting possibilities as a material. Between typical open fronted storage bins and whole pallets, there are now a wide variety of storage aids made from it. The advantages are impressive:
– High stability with low dead weight: this reduces, for example, the need for high load-bearing capacity of shelves (much higher than the pure weight of the goods) and greatly simplifies the handling of empty aids. A wooden Euro pallet has a much higher tare weight than a corrugated cardboard pallet.
– Foldability and recyclability: Currently unused storage aids made of corrugated board take up incomparably less space during storage. As a result, the same quantities require significantly less space than conventional storage aids – or significantly more aids can be kept in stock with the same amount of space.
Due to their stability, high-quality specimens can also be unfolded and refolded several times, which further increases their flexible use. At the end of their life cycle, they are easy to recycle – where the material can be recycled multiple times.
– Low procurement costs: Compared to the more common materials of wood, plastic and metal, corrugated storage aids are significantly cheaper across the board. They therefore tie up less capital when in storage and are not an insubordinate financial burden, even with a shorter service life due to rough handling.
Last but not least, the image should be considered here: Corrugated board has a comparatively low environmental and climatic footprint. It can therefore make warehouse operations more sustainable overall and thus generate a positive advertising impact – free from any suspicion of greenwashing.
Thinking about the topic of automation
As already mentioned, human employees are subject to strict legal criteria with regard to truly universal flexible deployment. Much of this can be negated through intelligent planning, but not everything.
In addition, one thing must always be considered in the present and foreseeable future: the shortage of personnel. A combination of very different causes ensures this. They include, among other things, the precarious demographic situation as well as education policy and, last but not least, a poor image of many physical as well as apprenticeship jobs – such as the jobs of pickers and packers or, more generally, warehouse logistics specialists.
The standing of the logistics giants is an aggravating factor here. In many cases, they are able to convince additional personnel by offering more attractive conditions. Smaller companies and warehouses are at a disadvantage because, for example, they cannot offer pay above the standard rate or non-monetary amenities.
As a result, many companies cannot count on finding enough staff in the foreseeable future. Especially not to be able to absorb spontaneous phases of high workload. Given this, more automation should definitely be an option worth considering.
Tips and best practices
If you immediately think of picking robots when you hear the term “warehouse automation,” you’re not wrong, but you’re already several steps too far. Neither are these robots the first nor only option for warehouse automation. Moreover, this transformation is also not something that can only be done completely or not at all. On the contrary, automation in the warehouse sector is highly scalable and thus offers rich opportunities for pinpoint deployment.
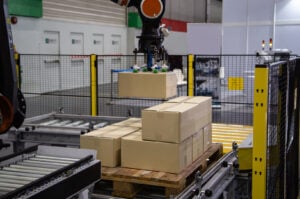
stock.adobe.com © Itsanan
The most important action, however, is the first step: analyzing in which areas the staff shortage is particularly pressing – even if it is only during periods of high capacity utilization. Sometimes it can emerge that what is needed is not so much physical automation with the help of machines or robots, but merely digital automation of processes – for example, through automated scanning at goods receipt instead of manual procedures.
Likewise, small physical measures can help a lot – for example, the principle of color picking:
– Several orders are processed simultaneously by one picker. Each of them has its own color code.
– The picker can see what he has to pick and to which of the orders it belongs by means of correspondingly illuminated color markings at the storage locations.
In contrast to the principle of light picking, this allows several orders to be processed at the same time.
In addition, there are further levels of automation below full-fledged warehouse robots, which, for example, handle the entire putaway or picking autonomously. Autonomous mobile robots” are currently the most important development here. They are the successor to classic driverless transport systems. In contrast to these, fixed tracks are no longer necessary – this makes the vehicles much more flexible in their use.
Due to the complexity, however, warehouse operators should seek professional advice; not so much from the representatives of individual suppliers of such automation technologies, but from neutral experts. This is necessary not least because each of these technologies, despite all the increase in flexibility, must of course be considered from the point of view of financial amortization:
It’s true that an autonomous mobile robot doesn’t mind running 24-hour shifts or hanging unused at the charger for two days. However, since many of these systems still incur high one-off costs, it must be carefully calculated whether they really provide more flexibility with lower permanent costs than human employees in the long term.
Examine alternative, modular storage systems
Most shelving and similar storage systems are fixed in place. At most, the individual levels can be adjusted in height – but even that often only with some effort.
However, there may well be rush phases in a warehouse in which only a fraction of the goods are actually stored after delivery before they are dispatched. In such cases, pallets and the like are unloaded and immediately “broken down” by pickers to be handled by packers – at least to a large extent.
In such situations, classic racking systems not only take up unnecessary space, but for this very reason can even inhibit faster processing without intermediate storage.
If this has already been done, the question should be whether these storage systems are still up to date in this company.
Tips and best practices
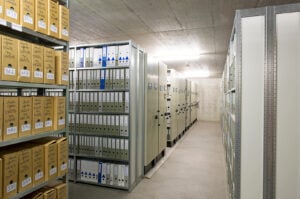
stock.adobe.com © kk_images
At this point, specific reference should be made to movable shelf storage systems. Very similar to what has been the case in large file warehouses for more than a century, these racks are stored on rails and are thus movable in one dimension. They can be used in two ways:
- traditional: in this case, there is only one aisle ready for the entire shelving area. The rest of the space is completely occupied by the shelves. To reach a shelf, all other shelves must be pushed away, thus forming an aisle there. This option maximizes the available storage space. In practice, however, it is only suitable for goods that are moved less frequently, as the constant moving is very time consuming.
- flexible: as usual, there is one aisle between each two racks. However, during busy periods or when other reasons require it, only a certain part of the shelves is used. The rest of the shelves – without goods or only with goods that are not needed – are pushed together completely.
Since such systems are now available for very high loads, it is an interesting option for warehouses of various orientations.
Summary and conclusion
A modern warehouse must be able to adapt within a short time to both greatly increased requirements and fluctuations in demand. Particularly in today’s world, where speed is of the essence in logistics, maximum flexibility is an important cost factor. This can be implemented very effectively and personalized thanks to a wide range of options.