Das beste, flexibelste und günstigste Lager ist zweifellos eines, das gar nicht benötigt wird. Dies ist der Hauptgrund, warum speziell in produzierenden Unternehmen die Just-in-Time-Fertigung Einzug hielt und heute eine globale Bedeutung hat. Allerdings ist das Prinzip schlichtweg nicht für jede Branche optimal – oder sogar überhaupt umsetzbar.
In solchen Fällen ist die Lagerhaltung ein unverzichtbarer Part der gesamten unternehmerischen Tätigkeit oder sogar ihr Kern. Allerdings bedeutet das keineswegs, dass hier keinerlei Optimierungen hinsichtlich verstärkter Flexibilität mehr möglich sind. Die folgenden Tipps beweisen das im Detail.
Warum das moderne Lager im Höchstmaß flexibel sein muss
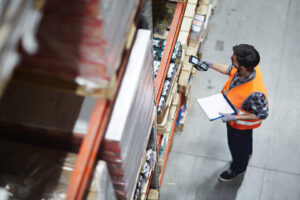
Die heutige Welt ist äußerst schnelllebig und dadurch weniger präzise vorhersagbar geworden. Dies gilt im unternehmerischen Bereich in einem ganz besonderen Ausmaß. Das macht unvorhergesehene Ereignisse zumindest wahrscheinlicher – mit der Pandemie und den Verwerfungen durch den Ukraine-Krieg als wohl prominenteste Beispiele der jüngsten Vergangenheit.
Im Prinzip existieren von der Herstellung der Einzelteile eines Produkts bis zu dessen Auslieferung an den Endabnehmer mehrere Positionen, an denen es zu Störungen kommen kann. Einen wesentlichen Anteil daran hat die Globalisierung – selbst, wenn sie an anderer Stelle viele Vorteile ins Feld führen kann.
Neben solchen möglichen (und vielfältigen) Störungen der Lieferketten kommen heute noch andere Positionen hinzu, etwa:
- schnelllebiger und sprunghafter gewordene Kundeninteressen bzw. -loyalitäten,
- geringere Gewinnmargen und dadurch weniger finanzieller Spielraum in Form von Reserven,
- größere Saisonalität von Waren bzw. dem Interesse daran sowie
- Fachkräftemangel und dadurch geändertes Mitarbeiterverhalten.
All das und noch mehr kann in unflexibles Lager nicht nur an seine Grenzen bringen, sondern es zu einem regelrecht schädlichen Faktor in einem Unternehmen machen. Beispielsweise dann, wenn aufgrund einer zu geringen Flexibilität eine enorme Menge „totes Kapital“ in Form von Waren gebunden ist. Oder dann, wenn die ganze Lagerorganisation es erschwert bzw. verunmöglicht, rasch auf stark steigende Nachfrage zu reagieren.
Ein moderner Lagerbereich muss daher eine möglichst große Flexibilität leisten können. Nur dann kann er sich verschiedenen Ereignissen anpassen – ohne jedoch die Fähigkeit zu verlieren, auf andere Vorkommnisse reagieren zu können. Konkret ergeben sich aus mehr Flexibilität drei starke Vorteile, die auf sämtliche Herausforderungen der heutigen Zeit eine Antwort liefern können:
-
Die heutige Geschäftswelt sorgt in vielen Lagern für eine teils sehr rasche und extreme Abfolge von Zeiten unterschiedlicher Auslastungen.
stock.adobe.com © ChlorophylleTransparenz: Es sind ständig Echtzeitinformationen vorhanden. Dadurch lässt sich jede Ware vollständig nach- und zurückverfolgen. Es droht niemals Konfusion und davon ausgelöste weitere Schwierigkeiten.
- Anpassungsfähigkeit: Ein flexibles Lager kann sich auf wechselnde Marktveränderungen auf beiden Seiten der Lieferkette einstellen – kurzfristig und zu geringsten Kosten.
- Effizienzsteigerung: Die gesamte Planungs- und Prozesskette wird vereinfacht und beschleunigt, da das flexibel aufgestellte Lager unterschiedliche Durchsatzgeschwindigkeiten gestattet.
Dabei sei unterstrichen, dass es sich hierbei sozusagen nur um „Obergruppen“ von Vorteilen handelt. Zu jedem davon gehören verschiedene weitere, damit verknüpfte Vorteile – etwa geringere Kostenbindung, mehr Einnahmen und weniger Abhängigkeit von Personal. Doch was können Unternehmer diesbezüglich praktisch veranlassen?
Das Lager-Layout ständig überprüfen
Ob Ersatzteillager eines Handwerksbetriebs oder riesiges Versandlager eines Online-Händlers: Jedes Lager hat nur eine limitierte Gesamtfläche. Sie setzt sich zusammen aus
- dem eigentlichen Lagerplatz, etwa für Regale,
- den zwingend nötigen Verkehrsflächen dazwischen,
- dem Bereich für das Picking und Verpacken bzw. anderweitiges Fertigmachen für den Versand und
- einem Ein- und Ausladebereich.
Damit ist bereits nur ein Teil des gesamten Raumes nur für die Lagerung an sich reserviert. Der Rest hingegen wird für die zwingend nötigen weiteren Prozesse rund um das Lagern benötigt.
Dieser Raum ist fest vorgegeben. Eine Erweiterung ist zwar möglich, ist jedoch – etwa im Fall eines Anbaus oder einer Hallenerweiterung – zumindest mit sehr hohen Kosten verbunden. Sofern die Firma nicht selbst die nötigen Erweiterungsflächen besitzt, sind diese zusätzlich zu erwerben. Das ist stets teuer und kann aus verschiedenen Gründen sogar gänzlich unmöglich sein.
Allerdings sollte eine räumliche Erweiterung stets nur als letzte Option angesehen werden. Denn hinsichtlich des Layouts kann selbst auf gleichbleibender Fläche viel unternommen werden, um die Prozesse zu flexibilisieren und/oder zu beschleunigen.
Tipps und Best-Practices
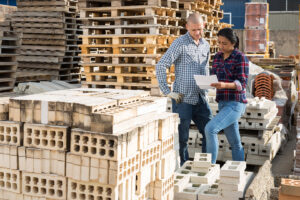
stock.adobe.com © JackF
Kern eines optimierten Lager-Layouts sind zwei Dinge:
- Verkürzte Wege und insgesamt erhöhtes Arbeitstempo – besonders bei Waren mit höherer Durchlaufrate.
- Maximale Ausnutzung der bestehenden Lagerflächen.
Hierzu empfiehlt es sich dringend, immer wieder die genutzte Lagerverwaltungssoftware zu konsultieren bzw. eine Software anzuschaffen, die ein integriertes Supply Chain Analytics Tool enthält.
Mit einem solchen Werkzeug lässt sich anhand der großen Datensätze sehr schnell herausfinden, ob das Lager insgesamt anpassungsfähig ist – und wo es mitunter hakt. Darauf basierend kann das Layout verbessert werden, primär durch folgende Maßnahmen:
- Änderung des Arbeitsflusses: Je nach Architektur bieten sich hier V-, I-, L- und U-förmige Herangehensweisen an, wobei die Enden der „Buchstaben“ jeweils für den Aus- und Einladebereich stehen. Je nach Warenart und erneut Gebäudearchitektur kann eine Umgestaltung eine deutliche Verbesserung bringen.
- Änderung der Lagerart: Grob unterschieden wird zwischen statischer und dynamischer Lagerung. Während bei ersterer jede Ware stets einen festen Lagerort hat, erfolgt das Einsortieren bei letzterem je nachdem, wie und wo gerade Platz ist – daher wird die dynamische Lagerung auch als „chaotische Lagerung“ bezeichnet. Sie lässt sich ohne ein leistungsfähiges Lagerverwaltungssystem kaum umsetzen, bietet dafür jedoch eine erwiesenermaßen deutlich gesteigerte Flexibilität und stets eine volle Platzausnutzung.
Hierbei ist es nicht zuletzt wichtig, verschiedene Herangehensweisen konkret für durchaus unrealistisch hohe Auslastungszeiten zu simulieren. Also dann, wenn nicht nur sehr viele Picker unterwegs sind, sondern ständig enorme Warenmengen neu eingelagert und ausgeliefert werden.
Die Arbeitszeiten im Rahmen des gesetzlich Möglichen flexibilisieren
Das Personal im Lager, oder besser gesagt die dafür gültigen gesetzlichen Arbeitszeit- und Pausenregelungen, sind vielfach ein Hindernis auf dem Weg zu mehr Flexibilität. Denn:
- Innerhalb von sechs Monaten darf die durchschnittliche tägliche Arbeitszeit nicht mehr als 8 Stunden betragen.
- Zwischen zwei Arbeitseinheiten muss eine ununterbrochene Ruhezeit von mindestens 11 Stunden liegen.
- Es gibt sehr hohe Hürden für eine Beschäftigung an Sonn- und Feiertagen. Zudem urteilten Gerichte schon mehrfach, dass nicht jedes hohe Arbeitsaufkommen Ausnahmen rechtfertigt – unter anderem gegenüber Amazon.
Dies und noch einige weitere Punkte können es sehr schwierig machen, für Stoßzeiten genügend Personal im Lager zu haben. Allerdings gibt es durchaus Möglichkeiten, im Rahmen der Legalität zu bleiben und dennoch sowohl Phasen sehr starker Auslastung als auch solche des totalen Gegenteils auffangen zu können.
Tipps und Best-Practices
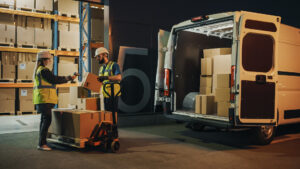
stock.adobe.com © Gorodenkoff
Dafür eignen sich primär die folgenden Herangehensweisen:
- Das Anordnen von Überstunden bei entsprechendem Ausgleich – das ist insofern interessant, weil der Ausgleich rechtssicher finanziell oder zeitlich erfolgen kann. Beispielsweise ist es möglich, die Mitarbeiter in Stoßzeiten Überstunden anhäufen zu lassen und diese danach per Anordnung abzubauen. Hier sei auf die Regelung verwiesen: Die täglichen 8 Stunden müssen lediglich im Schnitt eines halben Jahres bzw. 24 Wochen geleistet werden.
- Feste Zusammenarbeit mit Zeitarbeitsfirmen – insbesondere solchen, die sich auf das Vermitteln von erfahrenem Lagerpersonal eingestellt haben.
- Der Aufbau eines festen Pools von flexibel einsetzbaren „Saisonkräften“. Hier existieren vielen Menschen, die nur zeitweilig eine derartige Arbeit benötigen und die damit verbundene Flexibilität sogar zu schätzen wissen.
- Das Anordnen von Schichtarbeit ist unter einigen Voraussetzungen grundsätzlich rechtssicher möglich. Ebenso ist es durchaus möglich, diese Schichtarbeit nur für kurze Zeiträume zu fahren, um danach wieder zu einem herkömmlichen Modell zurückzukehren.
Letztendlich ist selbst im Rahmen der Gesetzesvorgaben vieles machbar, wenn Betriebsrat und Mitarbeiter mitspielen. Die Chancen dafür steigen, das zeigt die Erfahrung, wenn Arbeitgeber sich diesbezüglich fair geben. Das heißt, Mehrleistung entsprechend vergüten und Mitarbeiter tatsächlich nachhause schicken, wenn es wenig zu tun gibt – statt krampfhaft alternative Arbeiten zu finden.
Leichter einsetz- und austauschbare Lagerhilfsmittel nutzen
Unter den Begriff Lager- oder Ladehilfsmittel fällt alles, was dabei hilft, Waren leichter zu bewegen, einzulagern oder zu besser zu handhabenden Einheiten zusammenzufassen.
Die Herausforderung aus Sicht eines insgesamt flexibleren Lagerbereichs besteht aus einer Diskrepanz:
- Einerseits müssen die Lagerhilfsmittel stets in ausreichender Stückzahl vorhanden sein – und zwar im Höchstmaß spontan, damit auf steigende Bedarfsänderungen rasch reagiert werden kann.
- Andererseits sollten dieselben Lagerhilfsmittel bei Nichtgebrauch möglichst wenig Platz einnehmen, damit kein wertvoller Raum für die tatsächlichen Waren verlorengeht.
In vielen Unternehmen führt deshalb kein Weg daran vorbei, ein regelrechtes „Lager für Lagerhilfsmittel“ einzurichten. Das mag notwendig sein, verkompliziert aber in der Praxis vieles. Denn naturgemäß muss ein solches „Lager im Lager“ ebenso korrekt in die gesamten Prozesse eingebunden werden.
Tipps und Best-Practices
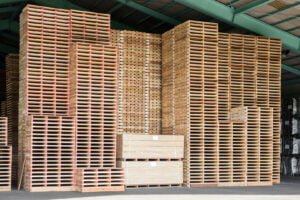
stock.adobe.com © lastpresent
Im Vergleich zu anderen Optionen bei der Flexibilisierung des Lagerbereichs gibt es hier nur eine wirklich tragfähige Lösung: Es sollte möglichst umfassend auf Lagerhilfsmittel gesetzt werden, die im unbenutzten Zustand so wenig Raum wie möglich verbrauchen, dennoch eine vergleichbare Belastbarkeit und Handhabung wie herkömmlichere Mittel aufweisen.
Insbesondere in überdachten Lagern bietet Wellmappe als Material mehrere interessante Möglichkeiten. Zwischen typischen Sichtlagerkästen und ganzen Paletten gibt es mittlerweile verschiedenste Lagerhilfsmittel, die daraus bestehen. Die Vorteile sind bestechend:
- Hohe Stabilität bei geringem Eigengewicht: Das reduziert beispielsweise die Notwendigkeit zu hoher Tragkraft von Regalen (deutlich höher als das reine Warengewicht) und vereinfacht die Handhabung leerer Hilfsmittel erheblich. Eine Holz-Europalette hat ein wesentlich höheres Eigengewicht als eine Wellpappe-Palette.
- Faltbarkeit und Recyclingfähigkeit: Momentan unbenutzte Lagerhilfsmittel aus Wellpappe beanspruchen bei der Lagerung ungleich weniger Raum. Dadurch benötigen gleiche Mengen deutlich weniger Fläche als herkömmliche Lagerhilfsmittel – oder es können bei gleichbleibender Fläche deutlich mehr Mittel vorrätig gehalten werden.
Aufgrund der Stabilität können hochwertige Exemplare zudem mehrfach aus- und wieder zusammengefaltet werden, was die flexible Nutzung weiter erhöht. Am Ende ihres Lebenszyklus sind sie leicht zu recyceln – wobei das Material mehrfach rezykliert werden kann.
- Geringe Beschaffungskosten: Im Vergleich mit den gängigeren Materialien Holz, Kunststoff und Metall sind Wellpappe-Lagerhilfsmittel durch die Bank deutlich günstiger. Sie binden daher in eingelagertem Zustand weniger Kapital und sind selbst bei kürzerer Lebensdauer durch ruppige Behandlung keine unbotmäßige finanzielle Belastung.
Nicht zuletzt sollte hierbei das Image betrachtet werden: Wellpappe hat einen vergleichsweise geringen ökologischen und klimatischen Fußabdruck. Sie kann daher den Lagerbetrieb insgesamt nachhaltiger machen und damit eine positive Werbewirkung generieren – frei von jeglichem Verdacht des Greenwashings.
Über das Thema Automatisierung im Lagerbereich nachdenken
Menschliche Mitarbeiter unterliegen, das wurde bereits angesprochen, strengen rechtlichen Kriterien, was einen wirklich universell flexiblen Einsatz anbelangt. Vieles davon lässt sich durch intelligente Planung zwar negieren, aber nicht alles.
Außerdem muss in der heutigen und absehbaren zukünftigen Zeit stets eines bedacht werden: der Personalmangel. Dafür sorgt eine Kombination aus sehr unterschiedlichen Ursachen. Sie umfassen unter anderem die prekäre demografische Situation ebenso wie Bildungspolitik und nicht zuletzt ein schlechtes Image vieler körperlicher sowie Lehrberufe – wie es die Jobs von Pickern und Packern bzw. allgemein Fachkräften für Lagerlogistik nun einmal sind.
Das Standing der Logistik-Giganten kommt hier erschwerend hinzu. Sie sind vielfach in der Lage, zusätzliches Personal durch attraktivere Konditionen für sich zu überzeugen. Kleinere Betriebe bzw. Lager haben dabei das Nachsehen, weil sie beispielsweise keine übertariflichen Vergütungen und nichtmonetäre Annehmlichkeiten bieten können.
Das Resultat: Viele Firmen können nicht darauf bauen, in absehbarer Zeit genügend Personal zu finden. Besonders nicht, um spontane Phasen großer Auslastung auffangen zu können. Angesichts dessen sollte mehr Automatisierung definitiv eine überlegenswerte Option sein.
Tipps und Best-Practices
Wer bei dem Begriff „Lager-Automatisierung“ sofort an Kommissionierroboter denkt, der liegt nicht falsch, ist aber bereits einige Schritte zu weit. Weder sind diese Roboter die erste noch einzige Möglichkeit der Lager-Automatisierung. Zudem ist diese Umwandlung ebenfalls nichts, was nur komplett oder gar nicht erfolgen kann. Im Gegenteil, die Automatisierung im Lagerbereich ist bestens skalierbar und bietet dadurch reichhaltige Möglichkeiten für einen punktgenauen Einsatz.
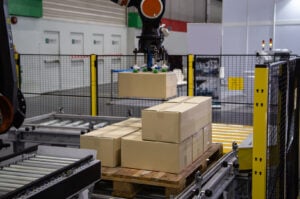
stock.adobe.com © Itsanan
Die wichtigste Handlung ist jedoch der erste Schritt: Die Analyse, in welchen Bereichen die Personalnot besonders drängend ist – und sei es nur während Hochauslastungsphasen. Mitunter kann sich hierbei herauskristallisieren, dass weniger eine physische Automatisierung mithilfe von Maschinen bzw. Robotern nötig ist, sondern lediglich eine digitale Automatisierung von Prozessen – etwa durch automatisiertes Scannen beim Wareneingang statt manueller Vorgehensweisen.
Ebenso können kleine physische Maßnahmen viel helfen – zum Beispiel das Prinzip des Color Pickings:
- Mehrere Bestellungen werden gleichzeitig von einem Picker bearbeitet. Jede davon hat ihren eigenen Farbcode.
- Über entsprechend aufleuchtende Farbmarkierungen an den Lagerorten sieht der Picker, was er kommissionieren muss und zu welcher der Bestellungen es gehört.
Im Gegensatz zum Prinzip des Light Pickings können hierdurch mehrere Bestellungen gleichzeitig bearbeitet werden.
Außerdem gibt es noch weitere Automatisierung-Abstufungen unterhalb vollwertiger Lagerroboter, die beispielsweise das gesamte Einräumen oder Picking autonom erledigen. Hier stellen derzeit „autonome mobile Roboter“ die wichtigste Entwicklung dar. Sie sind der Nachfolger klassischer fahrerloser Transportsysteme. Im Gegensatz zu diesen sind keine festen Spuren mehr nötig – das macht die Fahrzeuge deutlich flexibler einsatzbar.
Aufgrund der Komplexität sollten Lagerbetreiber sich jedoch fachmännisch beraten lassen; weniger von den Vertretern einzelner Anbieter derartiger Automatisierungstechniken, sondern von neutralen Experten. Das ist nicht zuletzt deshalb nötig, weil jede dieser Techniken bei aller Flexibilitätssteigerung natürlich unter dem Aspekt der finanziellen Amortisation betrachtet werden muss:
Zwar macht es einem autonomen mobilen Roboter nichts aus, 24-stündige Schichten zu fahren oder zwei Tage lang ungenutzt am Ladegerät zu hängen. Da viele dieser Systeme nach wie vor hohe Einmalkosten verursachen, muss jedoch sorgsam durchgerechnet werden, ob sie langfristig wirklich mehr Flexibilität bei geringeren Dauerkosten verursachen als menschliche Mitarbeiter.
Alternative, modulare Lagersysteme prüfen
Die meisten Regal- und ähnlichen Lagersysteme sind ortsfest montiert. Höchstens die einzelnen Ebenen können in der Höhe justiert werden – doch selbst das oft nur mit einigem Aufwand.
Allerdings kann es in einem Lager durchaus Stoßphasen geben, in denen nur ein Bruchteil der Ware nach der Anlieferung noch tatsächlich eingelagert wird, bevor sie auf den Versandweg kommt. In solchen Fällen werden Paletten und Co. abgeladen und sofort von den Pickern „zerlegt“, um von den Packern gehandhabt zu werden – wenigstens weitgehend.
In derartigen Situationen nehmen klassische Regalsysteme nicht nur unnötigen Raum ein, sondern können aus genau diesem Grund sogar das schnellere Prozessieren ohne Zwischenlagerung hemmen.
Wenn das bereits geschehen ist, sollte die Frage im Raum stehen, ob diese Lagersysteme noch zeitgemäß in diesem Unternehmen sind.
Tipps und Best-Practices
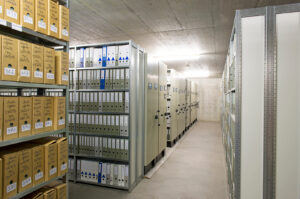
stock.adobe.com © kk_images
An diesem Punkt sei konkret auf verschiebbare Regallager verwiesen. Ganz ähnlich, wie es in großen Aktenlagern schon seit mehr als einem Jahrhundert der Fall ist, lagern diese Regale auf Schienen und sind dadurch in einer Dimension beweglich. Eingesetzt werden können sie auf zweierlei Arten:
- Traditionell: In diesem Fall steht für die gesamte Regalfläche nur eine einzige Gassenbereite zur Verfügung. Der restliche Raum wird gänzlich durch die Regale eingenommen. Um an ein Regal zu gelangen, müssen alle anderen Regale weggeschoben und somit dort eine Gasse gebildet werden. Diese Option maximiert die vorhandene Lagerfläche. In der Praxis eignet sie sich jedoch nur für seltener bewegte Waren, da das ständige Verschieben sehr zeitaufwendig ist.
- Flexibel: Es gibt, wie üblich, je eine Gasse zwischen zwei Regalen. In Stoßzeiten oder wenn andere Gründe es erfordern, wird jedoch nur ein gewisser Teil der Regale genutzt. Die restlichen Regale – ohne oder nur mit nicht benötigten Waren bestückt – werden gänzlich zusammengeschoben.
Da derartige Systeme mittlerweile für sehr hohe Traglasten angeboten werden, ist es eine interessante Option für Lagerhäuser unterschiedlichster Ausrichtung.
Zusammenfassung und Fazit
Ein modernes Lager muss sich binnen kurzer Zeit sowohl stark gestiegener Anforderungen als auch Nachfrageschwankungen anpassen können. Gerade in der heutigen Zeit, wo es in der Logistik vielfach auf Schnelligkeit ankommt, ist maximale Flexibilität ein wichtiger Kostenfaktor. Dies lässt sich dank verschiedenster Möglichkeiten sehr effektiv und personalisiert umsetzen.