How important is safety in your company’s logistical operations? Is the focus on compliance? Or, is safety actually integrated into your operations and culture?
That doesn’t happen quickly, and creating such a culture takes far more than catchy safety slogans. We break down the basics and have our top 5 picks on how to create a culture for more safety in logistics.
The Basics
Slips and trips
Slips and trips are the leading cause of serious injury in workplaces. While they may appear to be minor mishaps, studies note that 95% of slips and trips end in broken bones and can also serve as the precursor to more catastrophic accidents, such as falls from height. Employers are legally required to assess the danger of slips and trips and take reasonable precautions, such as providing enough lighting, providing slip-resistant footwear, and frequently inspecting floors for proper maintenance.
The majority of these steps are relatively straightforward and inexpensive to apply, and they will help reduce costly absences and injury claims caused by delay.
Fire protection
Fire is one of the most serious hazards to a business, and the need of considering fire safety has not diminished as a result of COVID-19. Indeed, companies should conduct a review of their fire risk assessment immediately to ensure that it accurately reflects any modifications made in response to COVID-19. For instance, if you have cut employee numbers or altered work schedules, you may have fewer Fire Marshals accessible. Fire awareness training is also a legal obligation, and it is probable that refresher training will be required upon return to work.
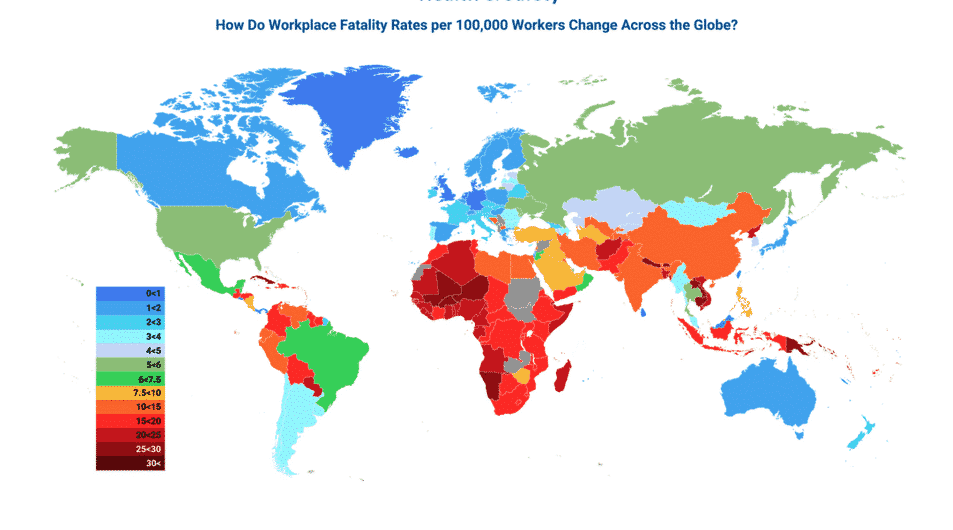
Premises
The legislation demands that all premises be safe for workers and guests to utilize. Electronic items, gas appliances, vents, and piping must be kept in a safe condition and examined on a regular basis by a qualified person. Especially during the pandemic Legionella hazards have become an issue, as the water in systems has not been utilized in months and now might harbor these bacteria. This might not only include offices but hotels, restaurants, and schools, as well as any other company that has been forced to close entirely or partially as a result of the lockdown. More broadly, it is a good idea to perform frequent walk-through inspections of your facilities to identify any harmful circumstances or behaviors and to take corrective action.
What can be done to improve the culture of safety in logistics?
Back up from the CEO
To begin, there must be unwavering support from the CEO, expressed loudly and frequently. Without this, cultivating a safety culture is a near-impossible task. The topic “safety” has to become part of the companies daily culture.
Measuring for motivation
Because you cannot improve what you cannot quantify, it is critical to track measures such as counting the time without incident. Distribute these findings broadly to foster a sense of shared responsibility for enhancing safety performance.
A toast to success
Strive for excellence, but never take it for granted. It’s essential to motivate and try to achieve a mutual goal. A challenge like “30 days without an incident” can engage the whole team. Commemorate the occasion and celebrate the success.
Collaborative safety audits
It is vital that safety audits are not considered as procedures carried out only to satisfy a statutory requirement. Avoid only marking boxes on an audit checklist.
Better engage associates at the local facility throughout the audit process; inquire about what works and what does not, and encourage suggestions. Demonstrate that you are not acting as “big brother” issuing a safety grade, but are committed to collaborating with the team to enhance safety performance.
Constant safety instruction and training
Slips, trips, falls, sprains, and strains — which combined account for the majority of workplace accidents in logistics facilities – are caused by poor technique or a lack of knowledge. Consistent training is required to reinforce established processes in a safety culture.
Conclusion
Many individuals consider health and safety in logistics to be a burdensome collection of paperwork, red tape, expense, and tedious rules and regulations that are difficult to comprehend and prevent you from running your business effectively. But when incidents or accidents occur they carry a hefty price tag both personally and for the company in terms of insurance costs, lost time, productivity dips and other negative consequences of injuries.