It’s impossible to envision a more complex series of manufacturing and distribution operations than those found in the semiconductor supply chain. There are numerous supply chain steps, beginning with material procurement and ending with silicon wafer manufacture, chip and processor assembly and testing, and last but not least – global shipment.
To further complicate matters, the semiconductor sector employs very capital-intensive manufacturing methods, volatile raw materials management, and the handling of high-value sensitive items. All of this requires the implementation of highly specialized and tightly aligned logistics services to support each component of the semiconductor value chain.
Today’s reality is, that every company relying on semiconductors and its related components is going to be constrained for at least until the end of 2022.
The logistics aspect in the semiconductor supply chain
Due to the worldwide nature of the semiconductor business, logistics and transportation capabilities must cover every continent and country, occasionally from inaccessible and distant regions to all major population centers. But since 2020 one of the biggest cautions to consider is whether supply chains will be able to keep up with growing demand.
Semiconductors are an excellent example of this. The lead times for many semiconductors are currently one year out, and these devices can be found in nearly all of our daily activities. Automobile and truck manufacturers around the world have reduced output due to a lack of semiconductors, as reported widely in the business and financial media. Most of these manufacturers have stated that they missed their 2021 goals and will do so in 2022. And it’s not just the automobile industry that’s in danger. Everything from electronics to medical gadgets to technology and networking equipment is expected to be affected by the chip shortages.
How Important are Semiconductors and Chips?
Fully understanding the importance of semiconductors to the modern world is sometimes complicated, as the devices are so small. But our current world is highly dependent on these tiny items. The most prominent example is the smartphone you use: Many smaller circuits comprising of millions of transistors are actually crammed into a few millimeters of silicon in a semiconductor device known as an integrated circuit (IC) or chip – the semiconductor. For electronics to operate and doing computations, these semiconductor devices are essential. As a result, semiconductors are the world’s fourth most-traded product, following crude oil and motor vehicle parts and refined oil.
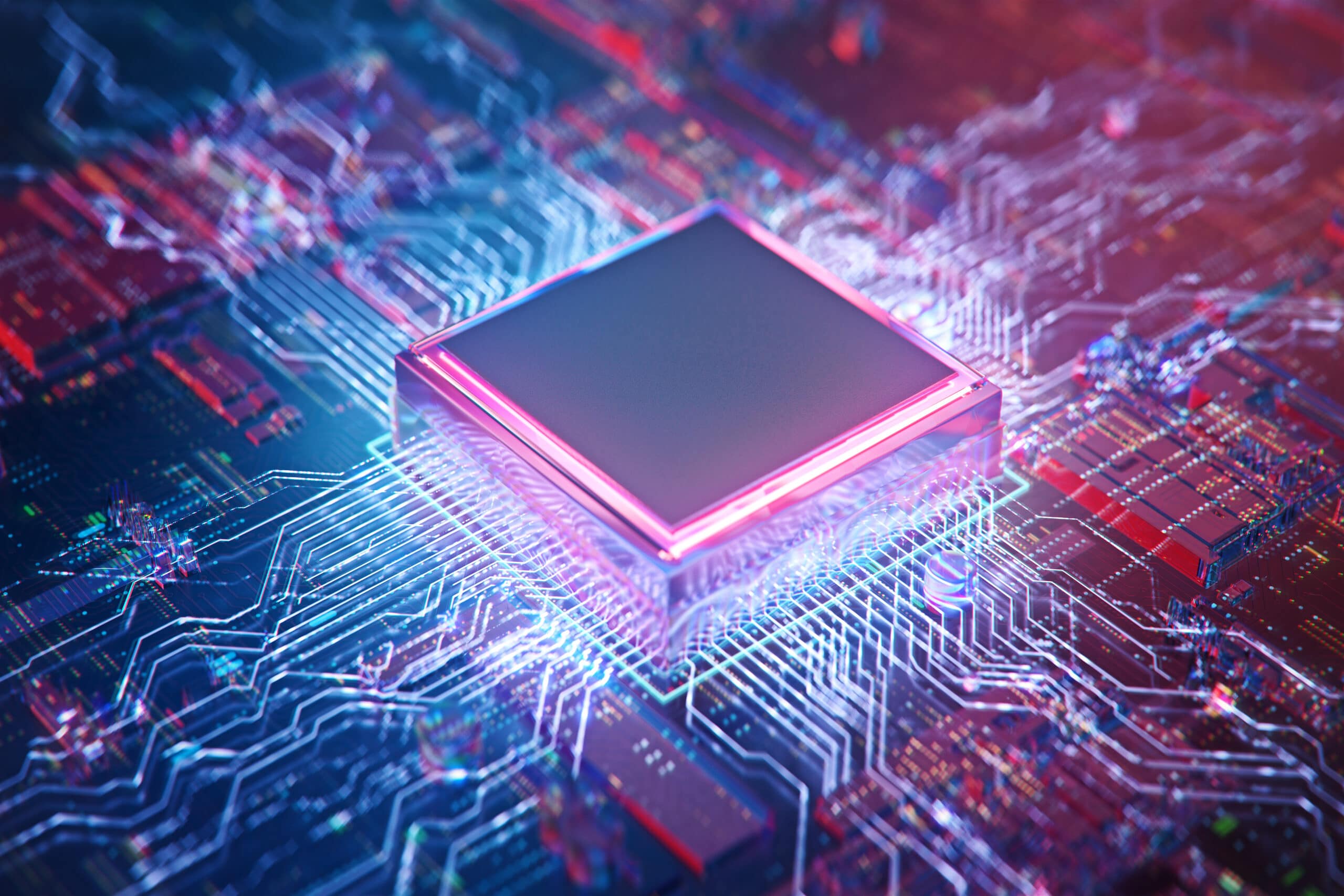
The vicious circle of the Semiconductor Supply Chain Shortage
To better understand where the semiconductor shortage came from and why it is about to stay we have to look back two years:
In 2020 the semiconductor industry had just overcome a longer downturn and was on the verge of a strong economic upswing. But then Covid-19 emerged and the automotive industry in particular feared weaker demand. Indeed, vehicle sales briefly collapsed in the spring of 2020. Almost in a panic, the chief buyers of the automotive companies canceled their orders to large chip manufacturers such as TSMC in Taiwan. However, that was to prove a momentous miscalculation.
Great demand for consumer electronics
But suddenly the demand for cars surged again unforeseen. However the canceled manufacturing capacities in the chip industry were no longer available to the vehicle industry. They had long been passed on to consumer electronics manufacturers, who experienced an above-average request since people were working from home, staying at home and surged the demand for smartphones, tablets, laptops and game consoles, she says. As a result, global chip stocks were quickly depleted.
Natural disasters and fires
The situation was exacerbated by a chain of unfortunate events: In February 2021, chip-makers such as Samsung, NXP and Infineon were forced to halt operations. One example was Texas, US, where heavy snowstorms hit, the power supply had failed, and the semiconductor fabrics weren’t able to be shut down in a controlled manner. This not only damaged production equipment, but also components of the plants’ infrastructure. There were also outages in Japan – in this case caused by natural disasters and fires in chip factories.
As if that weren’t enough, politics also contributed to the global chip shortage. Then-U.S. President Donald Trump had set out to limit the global influence of Chinese high-tech corporations such as Huawei and, among other things, imposed sanctions in the chip technology sector. As a result, Chinese companies made large-scale purchases of still-available chips and manufacturing equipment.
Does the semiconductor shortage affect the road freight transport industry?
For the automotive sector, it means that new vehicle sales will not be as high as manufacturers would like, simply due to production issues. This fact exacerbates the capacity problem the logistics sector already has. Due to the EU-Mobility Pack, a persistent driver shortage and now surging lack of new trucks, the road freight industry is forced to a halt.
The world’s second-largest producer of heavy goods vehicles, Volvo, stated that production sites had “to temporarily halt truck production corresponding close to a month”, while other manufacturers like Scandia had to shut down plants in three European countries for a week simultanously. A survey from Silf of Swedbank, found out that in 2021, sixteen percent of the companies have revised production plans downwards for Q3 and Q4 due to lack of material.
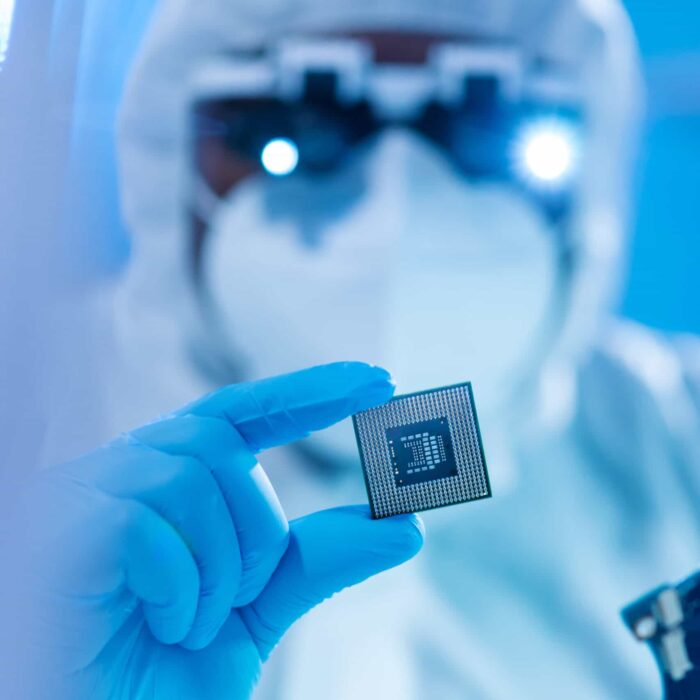
Understanding the Semiconductor Supply Chain
- Design: Device-specific or general-purpose semiconductor chip designs are created.
- Manufacturing (Front End): After being processed via a series of manufacturing procedures, the silicon wafers are sliced into individual chips (also called dies or devices).
- Manufacturing (Back End): Chips are stacked and packaged into packages that can be put on circuit boards at the manufacturing (back end) stage. A variety of electrical and thermal conditions are then applied to the packaged chips.
- End product Integration: Chips are integrated by electronics and equipment makers to produce end products for consumers.
- Consumption: The final product is sent around the world to enterprises, retailers, and consumers.
When will it end?
This question is asked all around the world at board rooms, whether big or small company. It’s a question heart from carriers and shipper, from around the globe. Supply chains are capacity-constrained and prices keep going up because people are spending disproportionately on consumer good, less on experiences and vacations. The pressure is turning any predictability upside-down, related to material availability, freight costs, labor scarcity, container shortages, and more. Fasten your seatbelt, we’re in for a long, bumpy ride. Many believe this is what the new normal will look like well into 2023.